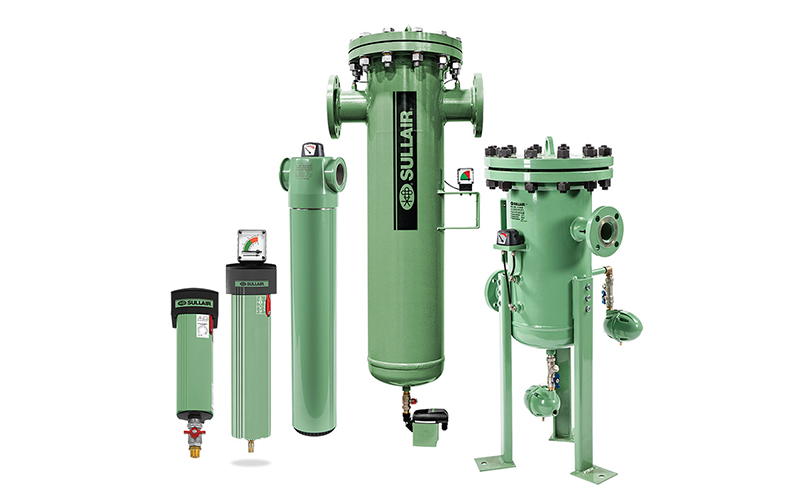
Choosing the Right Inline Compressed Air Filters
Not all compressed air is created equal. Neither are all compressed air systems.
Your compressed air needs to provide the flow, pressure and level of air quality required by your processes. A well-designed compressed air system supplies that air as economically as possible. A poorly designed system misses one or more of those goals.
So what makes a well-designed air compression system?
- An air compressor provides the flow and pressure.
- A compressed air dryer improves air quality by removing moisture.
- Compressed air filters improve air quality by not only removing some moisture but also other contaminants.
What is air quality?
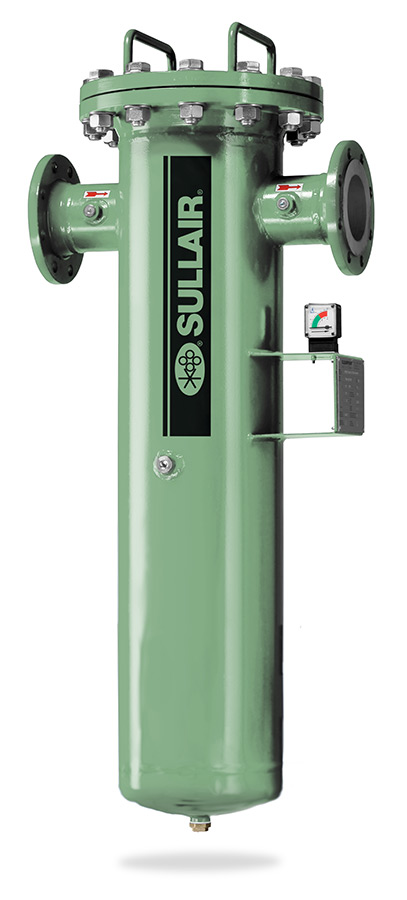
Air quality is a measure of how few contaminants are in the air stream. As mentioned above, compressed air dryers can help remove one type of contaminant—moisture. But filtration is needed to remove other types of contaminants from your air lines.
Types of contaminants removed by filtration
Particulates
Particulates are typically solid particles (e.g. dry and wet dust, pollen, and rust from pipe corrosion) and large liquid drops.
Aerosols
Aerosols include both oil aerosols and smaller droplets of water.
Vapor
Vapor consists primarily of oil and other hydrocarbons in a gaseous form.
Levels of compressed air filtration
The air quality level for all compressed air applications can be defined by the air quality classes in the ISO 8573-1:2010 standard. (See the post “The ABC’s and 1-2-3s of Air Quality Classes” for details about air quality levels and classes.) This standard specifies the allowed levels of contamination for each contaminant type at each air quality class. To meet these levels, you need to use the right types of air filters with the right degrees of filtration.
Types of compressed air filters
Particulate filters
Particulate filters remove particulates from the air stream by trapping contaminants on the media. The filter element design and material determine the size of the particles it can trap, so particulate filters have varying degrees of filtration.
Coalescing filters
Coalescing filters remove water and aerosols of liquids like oil by coalescence. Coalescence is the process of trapping smaller droplets along the media until they combine into larger drops that fall out of the air flow. The structure and type of media determine how much aerosol can be removed, so they also have varying degrees of filtration.
Combo particulate/coalescing filters
Some filter designs (e.g., Sullair SX series threaded and flange filters) act as both particulate and coalescing filters. You only need one filter with a single element to handle both types of filtration.
Activated carbon
Activated carbon filters are used to remove oil and hydrocarbon vapors from compressed air and reduce oil carryover to .003 mg/m³. These filters are most typically used where removing taste or odors is critical, e.g. food processing and pharmaceuticals.
Degrees of filtration for particulate and coalescing filters
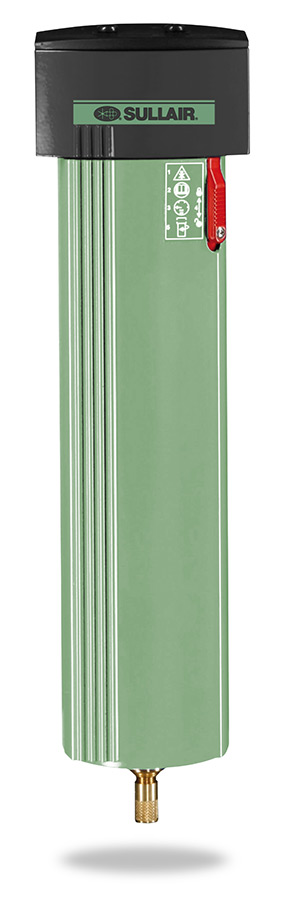
Coarse
Coarse particulate filters can only remove large particles from the air stream.
- Depending on filter materials and design, the smallest particles they can remove will be anywhere from 5 to 40 microns.
- Coarse coalescing filters can reduce oil carryover to as little as 5 mg/m³.
In most cases, coarse filters don’t provide high quality air. However, they can help remove moisture and keep large particles from fouling compressed air tools and instruments. (Unless those tools or instruments require higher quality air, of course.)
Fine
Typically, fine filters are the minimum size needed where applications or equipment need high quality air.
- Fine particulate filters can remove particles as small as 1 micron.
- Fine coalescing filters can limit oil carryover to .1 mg/m³.
Superfine/micro
Superfine filters are used when the highest quality air is needed; for example, for food production, pharmaceuticals, spray painting, and instrumentation.
- Superfine (sometimes called micro) particulate filters can remove particles as small as .01 micron.
- Superfine coalescing filters can limit oil carryover to .01 mg/m³.
Why not just use a single superfine filter? Or an active carbon one?
All degrees of filtration can collect larger particles and aerosols than they are optimized for. That might tempt you to just use filters with the highest degree of filtration needed—but you shouldn’t.
When filtering larger contaminants with finer filters, the buildup and loss of efficiency can happen much more quickly. (An active carbon filter could become clogged in hours, for example.) This can lead to unnecessary costs for replacement elements.
When should I replace my filter elements?
All filter elements have a maximum usable saturation point and eventually need replacing. Over time, contaminants build up on filter elements (including coalescing filters, as some solid particles, however small, are always present). Eventually, this buildup reduces the efficiency of the element. This efficiency loss causes larger pressure drops and allows more contaminants to pass through.
You shouldn’t try to save money by delaying or not replacing elements. If you don’t replace filter elements once they reached their maximum useable saturation point, your overall production costs could increase in three ways:
- Increased energy costs by requiring your compressor to run at a higher pressure set point.
- Increased production costs caused by additional contaminants ruining finished goods
- Increased equipment capital and/or maintenance costs by additional contaminants damaging equipment
Typical filtration in compressed air systems
These typical filtration examples for compressed air systems assume combo particulate/coalescing filters unless otherwise noted.
System without dryers
In systems without dryers, install a coarse or fine filter immediately after the compressor.
- Use a coarse filter if it meets both your particulate and aerosol requirements per ISO 8573-1:2010.
- Even if your processes don’t need to reach a particular ISO class, installing a coarse filter to remove excess particulates and oil can help protect your air tools.
- Use a fine filter if the coarse filter doesn’t meet both requirements.
If you need a stricter level of filtration, add a superfine filter after the fine filter.
Systems using refrigerated dryers
In systems using a refrigerated dryer, install a fine filter between the compressor and the dryer.
If you need a stricter level of filtration, install a superfine filter after the dryer.
If an active carbon filter is needed, install it after the superfine filter.
Systems using desiccant dryers
In systems using a desiccant dryer, install a fine filter between the compressor and the dryer.
If you need a stricter level of filtration, install a superfine filter between the fine filter and the dryer.
- You should consider installing the superfine filter even if you don’t need to meet a superfine filtration level. By removing more contaminants before the air reaches the desiccant bed, you can extend the life of the desiccant.
Immediately after the dryer, you should install a fine particulate filter (e.g. the Sullair SX, FXFRHT and FWFRHT particulate series filters) to remove any dust coming off the desiccant bed.
- You could install a combo filter instead, but no additional aerosols will be added by the desiccant bed. Therefore, a combo element would add an unnecessary expense.
If an active carbon filter is needed, install it after the fine particulate filter.
But how much filtration does my system need?
While typical filtration arrangements can serve as guidelines, your filtration should always be designed for your process needs. Too little filtration and the air stream could contain too many contaminants to provide the correct quality of air. Too much filtration and you could be paying more for your compressed air system and its upkeep than you need to.
Because filtration is so dependent on the specific needs of your processes and equipment, you should consult a local compressed air system specialist for help in setting up filtration for your compressed air system.